Fosroc Renderoc HB
Single component lightweight fibre and polymer modified concrete reinstatement mortar for high-build applications.
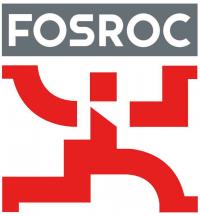
Uses:
For the reinstatement of large areas of concrete and for small, localised patch repairs. Renderoc HB is alkaline in nature and will protect embedded steel reinforcement. It is specifically designed for vertical and overhead high-build applications. The mortar is suitable where exceptional chloride and carbon dioxide resistance is required.
This mortar is approved for use with Norcure realkalisation. Refer to the Norcure note in the ‘Application instructions’ section of this data sheet for information.
Advantages:
- Lightweight formulation enabling extra high-build and thereby saving time and expense of multiple applications
- Reduces the need for formwork
- Can be applied by the wet spray process for fast, exceptionally high-build repairs with enhanced strength
- Extremely low permeability provides maximum protection against carbon dioxide and chlorides
- Excellent bond to the concrete substrate
- Shrinkage compensated
- Pre-bagged to overcome site-batched variations — only the site addition of clean water required
- Contains no chloride admixtures
- Renderoc Galvashield XP compatible
Description:
Renderoc HB is supplied as a ready to use blend of dry powders which requires only the site addition of clean water to produce a highly consistent, lightweight repair mortar. The material is based on Portland cement, graded aggregates, lightweight fillers and chemical additives and is polymer and fibre modified to provide a mortar with good handling characteristics, while minimising water demand. The hardened product exhibits excellent thermal compatibility with concrete and outstanding water repellent properties.
The low water requirement ensures fast strength gain and long-term durability.
Design criteria:
Renderoc HB can be applied in sections up to 80 mm thickness in vertical locations and up to 50 mm thickness in overhead locations in a single application and without the use of formwork. Thicker sections can be achieved by the use of formwork or can be built up in layers. Deep pockets can sometimes be filled in a single application depending on the actual configuration of the pocket and the volume of exposed reinforcing steel. The material should not be applied at less than 10 mm thickness.
Thicknesses generally greater than specified above can be achieved by spray application.
Standards compliance:
Renderoc HB, Nitoprime Zincrich Plus, Nitobond HAR and Nitobond AR have been approved by the British Board of Agrément, Certificate No. 98/3461.
Specification clauses:
Steel reinforcement primer:
The steel reinforcement primer shall be Nitoprime Zincrich Plus, a single component zinc-rich epoxy resin.
The primer shall be an ‘active’ type, capable of avoiding the generation of incipient anodes in the immediately adjacent locations. It shall be fully compatible with the Renderoc system of concrete repair.
Repair mortar:
The fibre and polymer modified reinstatement mortar shall be Renderoc HB, a single component cement based blend of powders to which only the site-addition of clean water shall be permitted. The cured mortar shall achieve a compressive strength of 22 N/mm², a flexural strength of 4.5 N/mm² and a tensile strength of 1.7 N/mm² at 28 days. Chloride diffusion coefficient shall be not greater than 2 x 10–10 cm²/sec (by the Taywood Method) and a 10 mm section of cured mortar shall provide a carbon dioxide barrier equivalent to not less than 800 mm concrete or 320 metres air (by the Taywood Method).
Properties:
The following results were obtained at a water : powderratio of 0.18 and temperature of 20°C.
Test method | Typical result |
Compressive strength (BS 6319, Pt 2: 1983 — dry cure): | 7 N/mm² @ 1 day 12 N/mm² @ 3 days 16 N/mm² @ 7 days 22 N/mm² @ 28 days |
Flexural strength (BS 6319, Pt 3: 1983): | 4.5 N/mm² @ 28 days |
Tensile strength (BS 6319, Pt 7: 1985): | 1.7 N/mm² @ 28 days |
Water absorption ISAT (BS 1881, Pt 5: 1970) | 10 minutes: 0.002 ml/m²/sec 2 hours: 0.001 ml/m²/sec |
Chloride diffusion (Taywood Method): | < 2 x 10–10 cm²/sec |
Carbon dioxide barrier Equivalent thickness of concrete to Renderoc HB @ 10 mm (Taywood Method): | 800 mm |
Equivalent thickness of air to Renderoc HB @ 10 mm (Taywood Method): | 320 metres |
Coefficient of thermal expansion: | 7 to 12 x 10–6/°C |
Setting time (BS 4551, Pt 14: 1980) | Initial set: 2 hours Final set: 5 hours |
Fire rating (BS 476, Pt 4: 1970): (Class 0 surface) | Non-combustible |
Fresh wet density: | Approximately 1400 kg/m³ dependent on actual consistency used |
Chemical resistance:
The low permeability of Renderoc HB severely retards chemical attack in aggressive environments. The cured mortar is highly i impermeable to acid gases, chloride ions, oxygen and water.